Ultrasonic Coating And ES Coating
Compared with Ultrasonic spray coating system and ES coating system
As one of the new energy sources with great development prospects around the world, PEMFC is known for its high conversion efficiency and low pollution. Protons exchange membrane fuel cell construction: MEA (PEM, catalyst and GDL) and bipolar plate. Proton exchange membrane is one of the most critical components of PEMFC, which directly affects the performance and life of the battery.
Proton exchange membranes can generate electricity, and catalysts must be coated on both sides of the film. The coating process must ensure that the thickness of the catalytic layer is uniform, and there are no defects such as cracks, particles, bubbles, edge effects, and so on. At present, the coating processes for mass production mainly include doctor blade, roll coating transfer, slit extrusion and ultrasonic spray systems.
Electrostatic spraying is to apply negative high voltage to the spray gun to form a high-voltage electrostatic field between the painted workpiece and the spray gun. When the electric field strength (E0) is high enough, the electrons at the tip of the spray gun needle have certain kinetic energy, which impacts the air near the muzzle to ionize air molecules to generate new electrons and ions, thereby locally destroying the air insulation and ionized air Move to the positive electrode under the action of the electric field force to produce corona discharge. The electron collision at the tip of the muzzle needle ejects the paint from the muzzle, causing the paint droplets to be negatively charged. If the paint droplets carry multiple negative charges at the muzzle and are repelled by the same sex, the paint droplets will further atomize, and the negatively charged.High paint quality requirements. Electrostatic spraying has certain requirements on the electrical properties of the paint, and it is easily affected by ambient temperature and humidity.
Therefore, in order to meet the requirements of electrostatic spraying, it is necessary to adjust the paint to the appropriate composition. Coating quality is easily affected. The uniformity of electrostatic sprayed coatings is greatly affected by the size and shape of the workpiece. Complex-shaped workpieces are affected by electric field shielding or uneven distribution of power lines, and the spraying quality is difficult to guarantee.
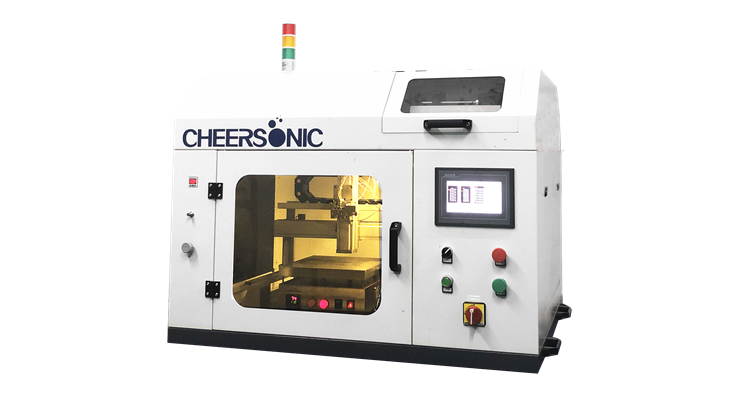
Ultrasonic coating technology creates highly uniform, repeatable and durable membrane. It operates through continues vibration from the nozzle to break up the agglomerated particles into evenly dispersed functional particles, maximizing surface area exposure of the catalyst to create higher electrochemical performance of coatings. And when using the ultrasonic spray coating technology apply catalyst coating to the membranes by adjusting the spray parameters (height, flow rate and frequency of the nozzle) to control the rate of water added, because it needs to keep the thin membrane moist and not deformed.
Cheersonic has committed to the research and development of various ultrasonic equipment for more than ten years. CENG-S, CENG-M and CENG-L developed by our company is basic, programmable micro material spray coating system. Various types of catalysts suspensions including the carbon black ink, PTFE binder, ceramic slurry, platinum and other precious metal can be sprayed by using this bench-top ultrasonic spraying system capable of programming and controlling x, y, z three-axis coordinated operation are deposited onto PEM fuel cells, GDL, electrodes, electrolyte membranes and SOFC to create maximum load and high cell efficiency. Precise and controllable liquid supply system compared with different types of customized nozzles, significant reduction in materials usage and producing the highly uniform durable, repeatable and durable coatings from R & D to medium-sized batch production. The body is small and easy to place, the spraying performance is stable, and the operation is convenient.