Project Description
Coating Gas Diffusion Layer
The gas diffusion layer plays an important role in supporting the catalytic layer, collecting current, conducting gas, and discharging reaction product water in the fuel cell. The gas diffusion layer materials commonly used in proton exchange membrane fuel cell electrodes are carbon fiber paper, carbon fiber woven cloth, non-woven cloth, and carbon black paper. The base materials of the gas diffusion layer in the research include carbon fiber paper, carbon fiber woven cloth, carbon fiber non-woven materials and carbon black paper, etc., but some metal materials are also used, such as a flat metal sponge — mesh metal nickel.
The selection of high-performance gas diffusion layer materials is conducive to improving the overall performance of the electrode. This material must meet the following requirements: 1. Uniform porous structure with good air permeability; 2. Low resistivity and strong electronic conductivity; 3. Structure Compact and smooth surface, reduce contact resistance, improve conductivity; 4. Have a certain mechanical strength, appropriate rigidity and flexibility, which is conducive to the production of electrodes, and provide stability of the electrode structure under long-term operating conditions; 5. Appropriate hydrophilicity /Hydrophobic balance, to prevent excessive moisture from blocking the pores and reduce the gas permeability; 6. It has chemical and thermal stability; 7. The manufacturing cost is low, and the performance/price ratio is high.
How to prepare a high-quality gas diffusion layer?
Ultrasonic coating technology creates highly uniform, repeatable and durable membrane. It operates through continues vibration from the nozzle to break up the agglomerated particles into evenly dispersed functional particles, maximizing surface area exposure of the catalyst to create higher electrochemical performance of coatings. And when using the ultrasonic spray coating technology apply catalyst coating to the membranes by adjusting the spray parameters (height, flow rate and frequency of the nozzle) to control the rate of water added, because it needs to keep the thin membrane moist and not deformed.
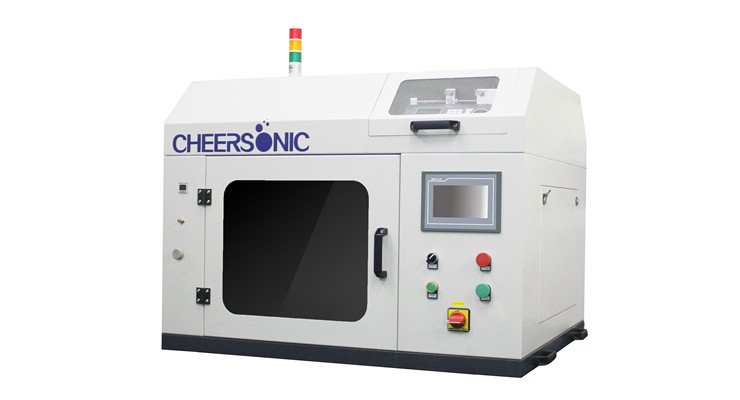
Cheersonic has committed to the research and development of various ultrasonic equipment for more than ten years. UAM4000L, UAM6000 and UAM8000 developed by our company is basic , programmable micro material spray coating system. Various types of catalysts suspensions including the carbon black ink , PTFE binder, ceramic slurry, platinum and other precious metal can be sprayed by using this bench-top ultrasonic spraying system capable of programming and controlling x, y, z three-axis coordinated operation are deposited onto PEM fuel cells, GDL, electrodes, electrolyte membranes and SOFC to create maximum load and high cell efficiency. Precise and controllable liquid supply system compared with different types of customized nozzles, significant reduction in materials usage and producing the highly uniform durable, repeatable and durable coatings from R & D to medium-sized batch production. The body is small and easy to place, the spraying performance is stable, and the operation is convenient.