Misunderstandings of Ultrasonic Welding Process and Solutions
Misunderstandings of Ultrasonic Welding Process and Solutions. At present, ultrasonic welding machines have been widely used in industries such as product packaging, cutting, riveting, embossing, and punching. The methods of use and equipment requirements are quite different. To talk about how to use the ultrasonic welding machine correctly in view of these misunderstandings, the following points should be paid attention to:
1. Misunderstanding of welding principle
There are quite a few people who have been engaged in ultrasonic welding for many years. There is a misunderstanding of the ultrasonic energy transfer. It is considered that sound waves are welded on the contact surface. In fact, this is a misunderstanding. The real welding principle is: after the transducer converts electrical energy into machinery, it is conducted through the workpiece material molecules, and the sound waves are The conductive acoustic resistance in a solid is much smaller than the acoustic resistance in the air. When a sound wave passes through the joint of the workpiece, the acoustic resistance in the gap is large, and the heat generated is quite large. The temperature first reaches the capacity point of the workpiece, and then a certain pressure is applied to weld the seam. The other parts of the workpiece will not be welded due to low thermal resistance. The principle is similar to Ohm’s law in electrical engineering.
Ultrasonic welding machines also have requirements for the material of the workpiece to be welded. Not all materials can be welded. Some people understand that any material can be welded. This is a big misunderstanding. Some of the different materials can be welded better, some are basically fused, and some are not fused. The melting point of the same material is the same, and it can be welded in principle, but when the melting point of the workpiece to be welded is greater than 350 ℃, it is not suitable for ultrasonic welding, because the ultrasonic melts the molecules of the workpiece instantly, and the judgment basis is If the welding fails within 3 seconds, another welding process should be selected. Such as hot plate welding. Generally speaking, ABS material is the easiest to weld, and nylon is the most difficult to weld.
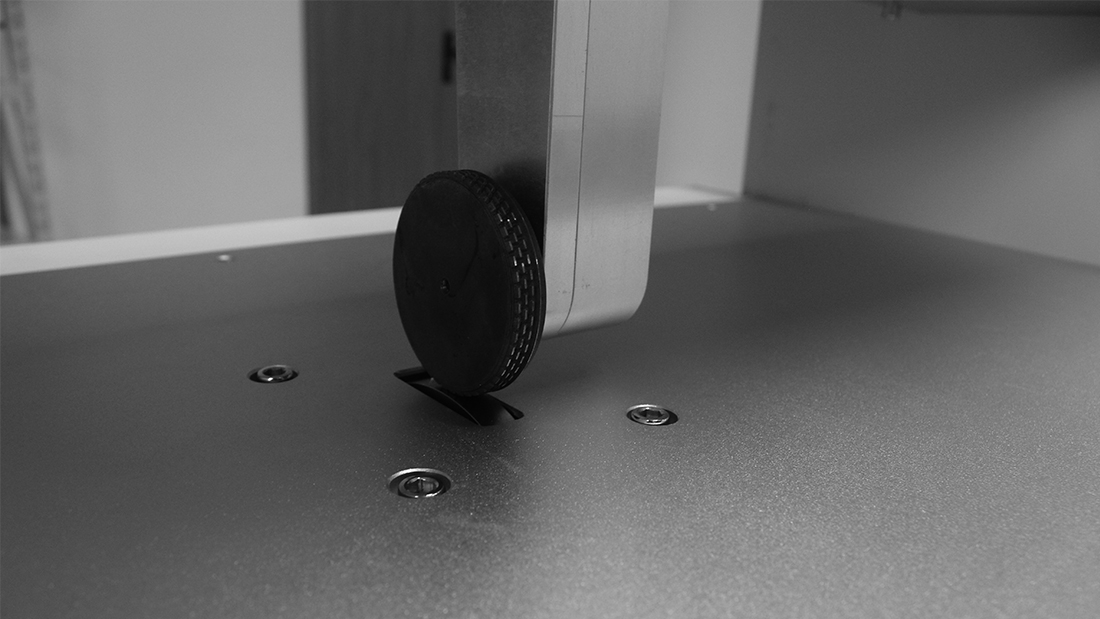
2. the process misunderstanding of welding workpieces
Ultrasonic energy bursts in an instant, the welding point should be dots or lines, and the transmission distance must be in line with the ultrasonic welding method. Some people think that as long as it is a plastic material, no matter how the joint surface can be welded well, this is also a misunderstanding. When the instantaneous energy is generated, the larger the joint area, the more serious the energy dispersion, the worse the welding effect, and even the welding is impossible. In addition, ultrasonic waves propagate longitudinally, and the energy loss is proportional to the distance. Long-distance welding should be controlled within 6 cm. The welding line should be controlled between 30-80 wire, and the arm thickness of the workpiece should not be less than 2 mm, otherwise it will not be well welded, especially for products that require airtightness.
3. the misunderstanding of welding structure
1) There are many types of ultrasonic molds (HORN). The shape of the workpiece determines the shape of the mold, but the size, curvature and material of each part must be strictly calculated. Some people mistakenly think that it is just a metal block. Whether the design is reasonable or not directly affects the mold’s efficiency, life, and product qualification rate, and in severe cases, it will directly burn out the generator. The material of the mold is generally magnesium-aluminum 7075, and some people use inferior materials or counterfeit 7075 to reduce costs. Regular mold manufacturers have a set of strict inspection procedures for incoming materials, and the processing dimensions are processed after computer software simulation and verification, so that the quality can be guaranteed. These processes cannot be done in general workshops. If the mold is not designed properly, the reaction problem is not obvious when welding small workpieces, and various drawbacks will appear when the power is high. In severe cases, the power components will be directly damaged.
2) The size of the ultrasonic output power is determined by the diameter and thickness of the piezoelectric ceramic sheet, the material, and the design process. Once the transducer is shaped, the maximum power is also shaped. Measuring the magnitude of output energy is a complicated process. It is not that the larger the transducer, the more power tubes used in the circuit, the greater the output energy. It requires a very complex amplitude measuring instrument to accurately measure its amplitude. Users have too much knowledge of ultrasound, coupled with the misleading of some sales staff, give consumers a misunderstanding. The amount of electrical energy consumed does not reflect the magnitude of the excess output power. For example, the low longitudinal energy produced and the large current consumption can only indicate the low efficiency of the equipment.
3) How much output power to use, the oscillation frequency, and the amplitude range should be considered according to the material of the workpiece, the area of the welding wire, whether there are electronic components in the workpiece, whether it is airtight, etc. It is mistaken that the greater the power, the better, this is also an issue misunderstanding. If you don’t know much about ultrasound, it’s best to consult a regular ultrasound manufacturer’s engineering and technical personnel. If possible, it’s best to communicate with the manufacturer on site. Don’t blindly follow the misleading of some informal ultrasound sales staff. At present, companies that produce related equipment are particularly mixed, most of which are family-style workshops, which mimic circuits mechanically and do not understand the working principles. The imitated equipment has the following fatal flaws. One is that the quality of externally purchased metamaterials cannot be guaranteed, and the second is that the core technology of the production process is not mastered. The equipment often exhibits instability when working at medium power and high power, and the product qualification rate is low. Sometimes the equipment is damaged. For example, the power transformer driving the transducer, the magnetic material parameters used cannot be measured, magnetic saturation magnetic flux density (Bs), magnetic induction intensity (Bm), effective permeability (Ue), residual magnetic flux density (Br), Coercivity (A/M), loss factor (tan£), temperature coefficient (au/K-1), the winding process is quite particular, including the vacuum immersion epoxy resin. These test equipment and production environment family factories cannot do it. Therefore, when purchasing ultrasonic welding equipment, it is best to understand the company’s situation first, do not blindly follow the salesperson’s praise, and do not just look at the price, only in this way can we reduce unnecessary troubles in the future.