DMFC Performance Optimization Program
DMFC Performance Optimization Program – DMFC Coatings – Cheersonic
Passive direct methanol fuel cell (DMFC) has a simple structure and has broad application prospects in mobile electronic devices such as mobile phones and PDAs. Improving the performance of membrane electrode (MEA), simplifying the stack structure and realizing pure methanol feed can effectively increase the energy density of the system, which is of great significance to the miniaturization of passive DMFC. Ultrasonic spraying is conducive to the formation of high metal loading catalysts and optimization of MEA preparation, and improves the performance of passive DMFC.
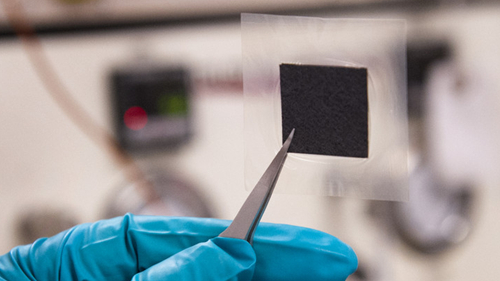
Although passive DMFC has the advantages of simple system structure, passive DMFC is at room temperature under work, methanol electrochemical oxidation rate is slow, electrolyte membrane conductivity is low, methanol and oxygen diffusion rate. In view of the problems of severe methanol penetration and insufficient catalyst activity, the improvement of solid electrolyte membranes, electrode catalysts and carriers has been ongoing. The activity of the catalyst is often greatly inhibited under low temperature conditions. The kinetics of methanol oxidation reaction is slower than that of hydrogen-oxygen reaction, so the noble metal catalyst loading is 5-10 times higher than that of PEMFC.
Inkjet printing and ultrasonic spraying gas diffusion electrode (Gas Diffusion Electrode, referred to as GDE) method and catalyst coated membrane (Catalyst Coated Membrane, referred to as CCM) method to prepare flexible MEA with carbon cloth as the diffusion layer material, by comparing the catalytic layer Different factors such as Nafion content, catalyst loading, hot pressure pressure, etc. Ultrasonic spraying can accurately control the Nafion content in the membrane electrode catalytic layer, reduce the thickness of the catalytic layer, and optimize the composition and structure of the MEA anode diffusion layer, and it allows large areas to be coated at high-speed with only minimal loss to coat catalyst suspension. However, the catalyst coating formed by Inkjet printing has poor uniformity and different thicknesses. A slightly rough film appears on the periphery of the module, and more serious cracks and peeling. The waste of materials cannot be ignored.
Cheersonic has committed to the research and development of various ultrasonic equipment for more than ten years. UAM4000L, UAM6000 developed by our company is basic, programmable micro material spray coating system. Various types of catalysts suspensions including the carbon black ink, PTFE binder, ceramic slurry, platinum and other precious metal can be sprayed by using these equipment. Cheersonic ultrasonic dispersion syringe pump is 25 ml glass syringe standard,by controlling module delivers electrical impulses to generate ultrasonic vibrations inside of syringe body, and duration and intensity of ultrasonic vibrations is user controlled to completely disperse and hold particles evenly suspended in solution for up to several hours.